In the world of metal fabrication, speed and precision are essential. However, when you introduce repetition into the equation, thousands of identical steel components (each expected to perform without failure), consistency becomes just as important. That’s where CNC profiling proves its worth.
For manufacturers, fabricators and engineers running repeat production, every cut matters. A small deviation could mean misaligned parts, expensive rework, or delays in assembly. Singleton Engineering offers CNC profiling services designed not only for accuracy and speed but also for reliability across high-volume orders.
Whether you’re supplying repeat batches for structural sections, OEM components, or ongoing infrastructure projects, CNC profiling gives you control and Singleton delivers it at scale.
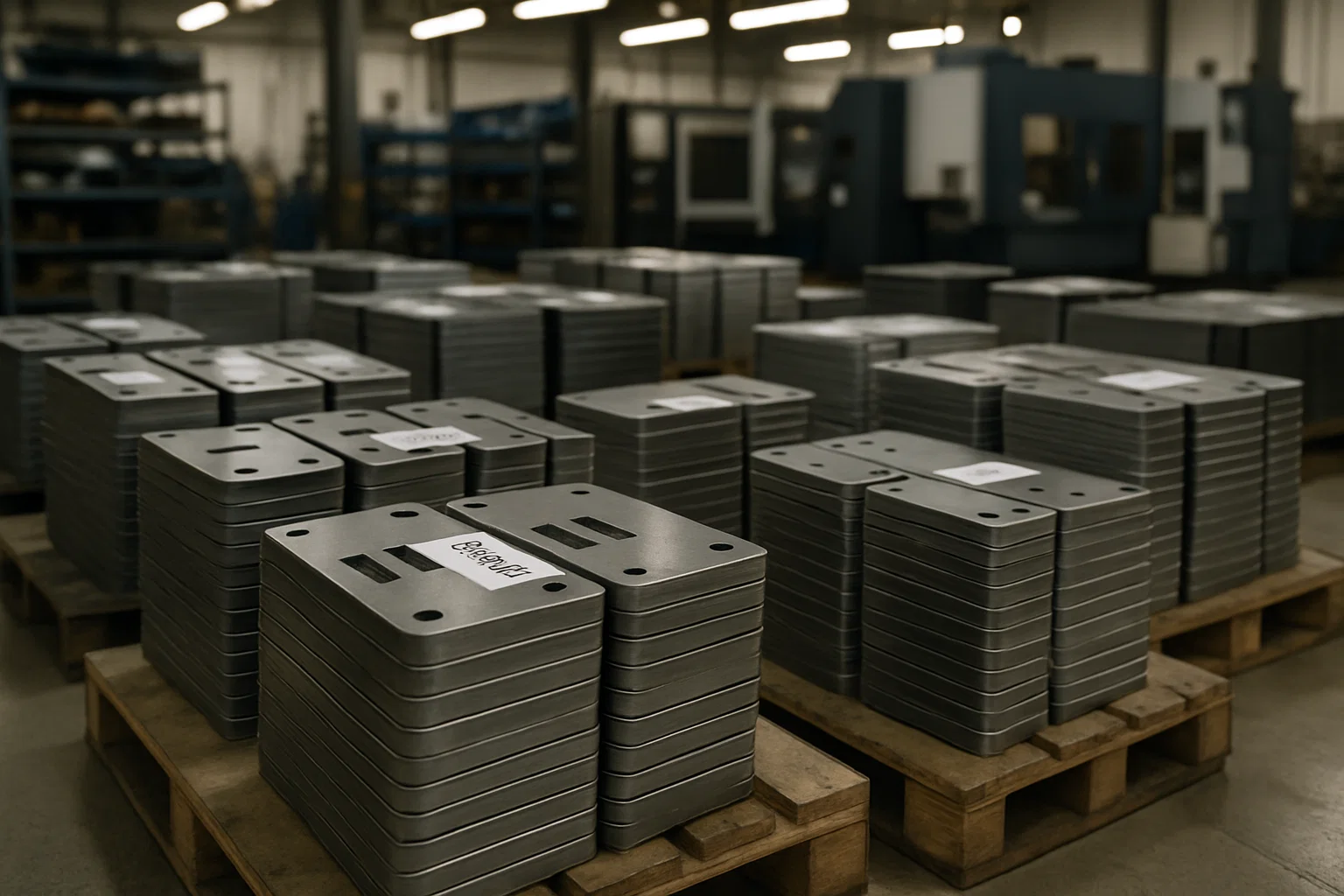
Why Repeat Production Demands Consistency
Many industries rely on the repeat manufacture of steel components. Construction firms often need hundreds of bracket sets, stiffeners, or cleats. Manufacturers might require thousands of profiled blanks to feed into robotic forming lines. Rail and infrastructure projects often have multiple phases across months or years, each requiring the same steel profiles delivered on demand.
In these environments, small discrepancies are costly. A millimetre off in profiling might not seem like much, but when that part is part of a bolted assembly or machine housing, the result is misalignment. That’s why dimensional accuracy is key.
With CNC profiling, digital instructions guide the CNC machine to create precise cuts with no variation between the first part and the thousandth. This ability to repeat profiles precisely is what sets CNC apart from manual or semi-automated methods.
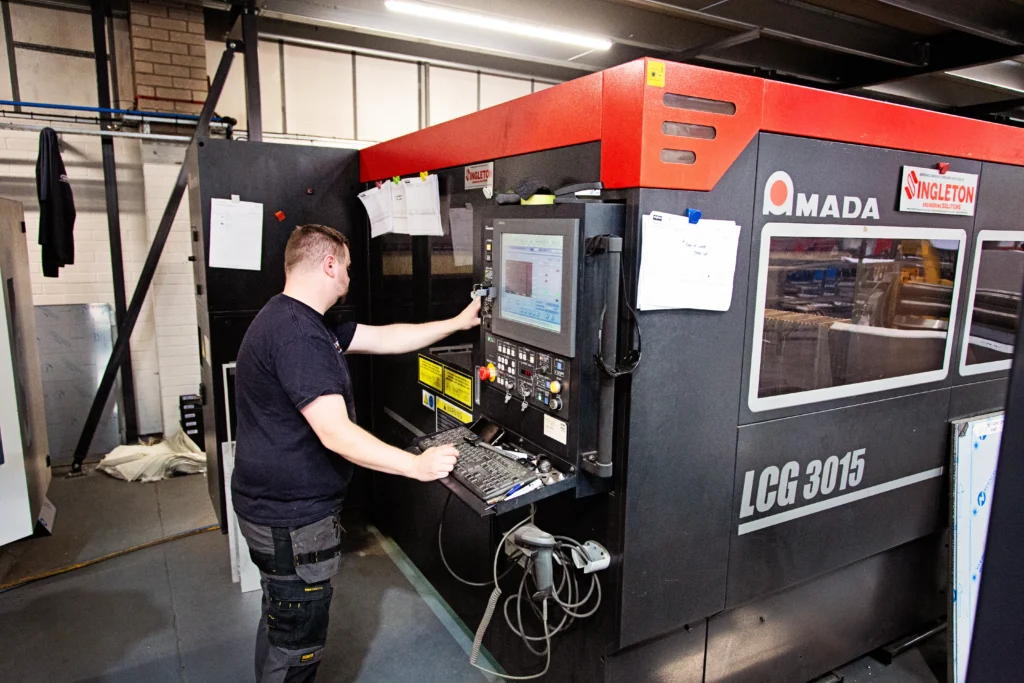
How CNC Profiling Guarantees Repeatable Accuracy
Computer Numerical Control (CNC) machines operate using programmed instructions. Once a design is finalised, often in the form of a DXF or DWG drawing, it’s entered into a CAM (computer-aided manufacturing) system. That data then guides the machine as it completes the cutting process.
The result is an extremely high degree of dimensional accuracy, typically within a fraction of a millimetre. More importantly, it means that the same profile can be reproduced indefinitely, whether that’s next week, next month, or next year.
At Singleton Engineering, our CNC milling machines and cutting tables are set up to deliver repeat production with minimal waste. We use CNC nesting software to optimise material usage and control cutting forces that could otherwise distort fine profiles. Every part we produce is traceable and archived for repeat batch runs.
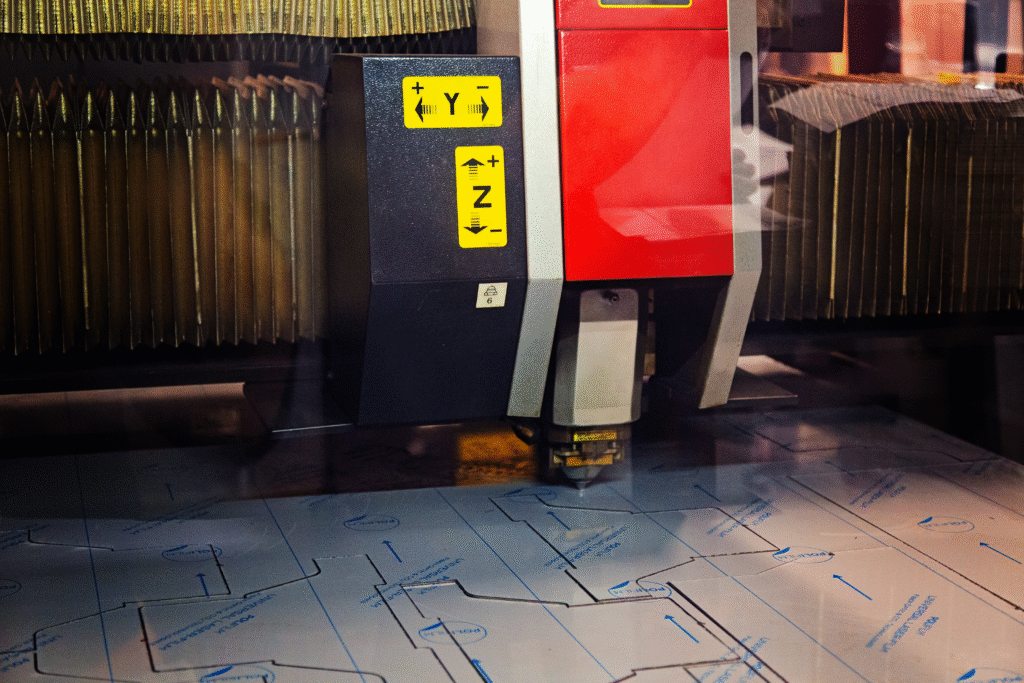
Meeting Volume Without Losing Precision
Volume and accuracy rarely go hand in hand with traditional profiling methods. Flame cutting is excellent for heavy sections but struggles with fine detail. Plasma cutting has improved over time, but the heat generated during the process can affect tolerances.
Laser cutting is known for its high precision and speed, making it ideal for thinner gauge materials and intricate designs. For thicker materials or stainless applications, waterjet cutting provides a cold-cutting alternative that maintains edge quality without thermal distortion. These waterjet machines are especially useful when profiling complex shapes in stainless steel grades like 304 or 316.
CNC profiling incorporates all of these technologies where relevant. At Singleton, we choose the right cutting method based on material thickness, feed rate, required finish and tolerance. This approach allows us to scale up production without losing control over quality.
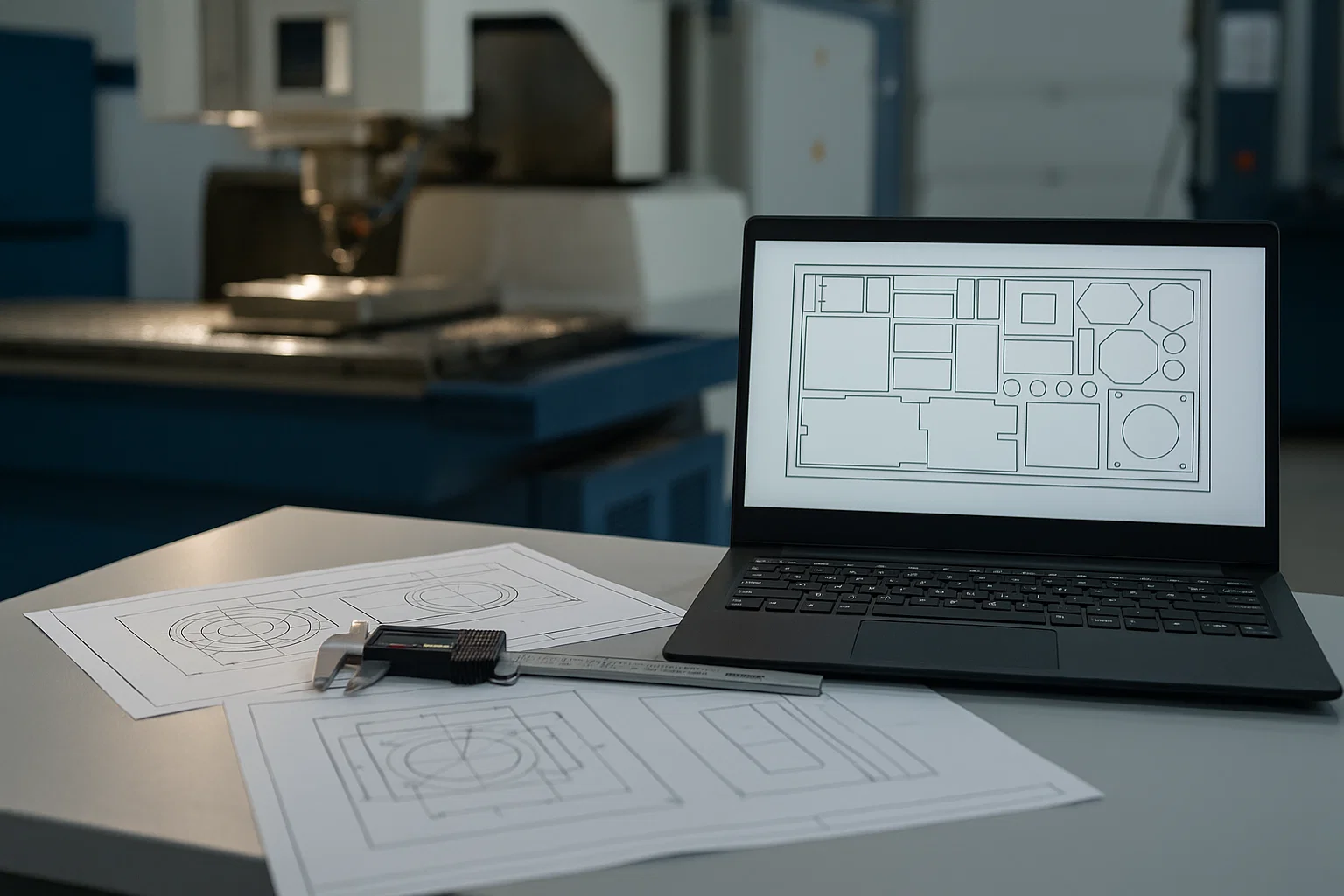
CNC Profiling and Production Planning
Repeat profiling isn’t just about cutting steel, it’s about how that service integrates into your production cycle. Singleton works with clients to plan scheduled releases, allowing consistent batch profiling without holding up their downstream operations.
Some clients order thousands of parts in one go. Others prefer to place smaller orders regularly but expect the same accuracy. In both cases, our profiling software stores the program, material specs and tooling settings to enable repeat runs with zero manual re-entry.
We also produce custom fixtures to prevent movement during cutting, especially when working with thin or small-profile parts. This improves overall cut quality and reduces variation between runs.
By integrating profiling with our fabrication workflow, we support various industries, including manufacturing, modular construction and precision engineering, helping them meet demand without sacrificing quality.
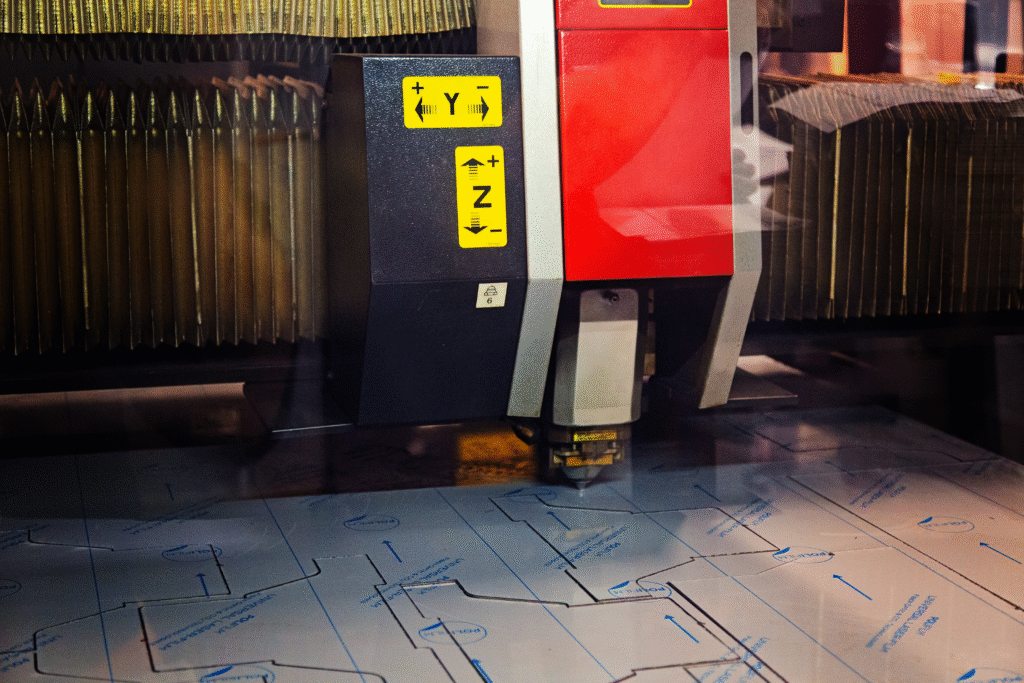
Advantages of CNC Steel Profiling for Repeat Jobs
The biggest advantage of CNC profiling in repeat scenarios is cost effectiveness. Once a part has been programmed, it can be produced repeatedly with little to no additional setup, reducing labour input and scrap.
Clients benefit from fast turnaround, accurate repeatability and the ability to scale volume when needed. Cutting speed can also be increased once tolerances are proven on a prototype run, meaning production gets more efficient over time.
Whether the requirement is for mild steel, aluminium, or stainless steel, CNC allows you to specify tolerances, hole positions and contours to suit your process. From light gauge steel to heavy base plates, every profile is delivered to match common grades and QA documentation.
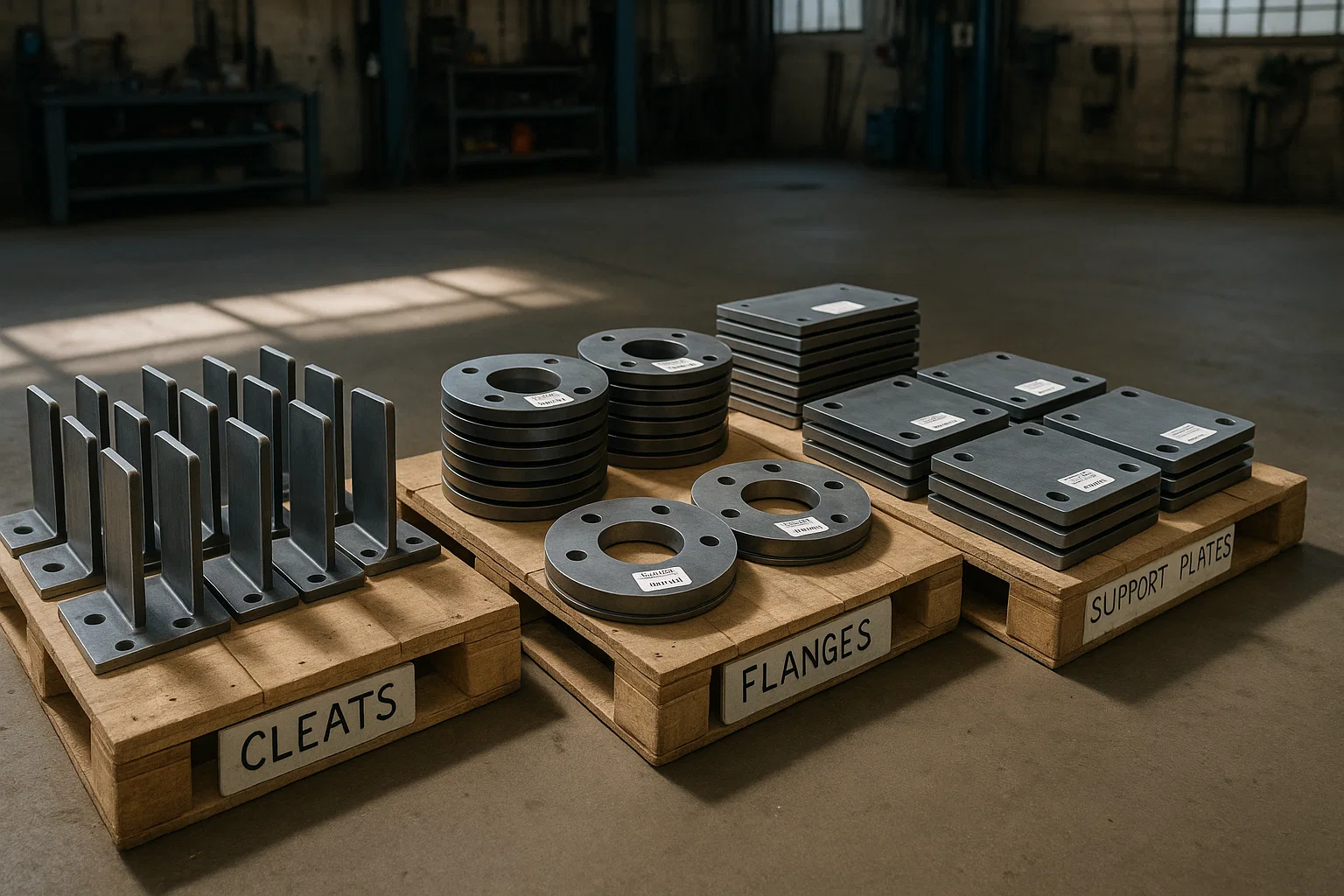
Real-World Applications in Repeat Steel Profiling
One of Singleton’s regular clients is an equipment manufacturer who requires hundreds of identical side panels in stainless steel for each production run. These panels feature precise bolt holes, cut-outs and edge bevels. The parts must align perfectly with sheet-metal frames that go through robotic assembly.
By using CNC profiling, we achieved better dimensional accuracy than their previous supplier and reduced lead time by holding ready-to-go programs. Over six months, we delivered over 4,500 parts without a single rejection, proof that consistent CNC cutting supports high-quality manufacturing.
In another case, we supported a modular building firm with steel floor brackets used across multiple sites. Batches were delivered just-in-time across six locations. The consistency in profile allowed installation teams to work faster, reducing downtime on site.
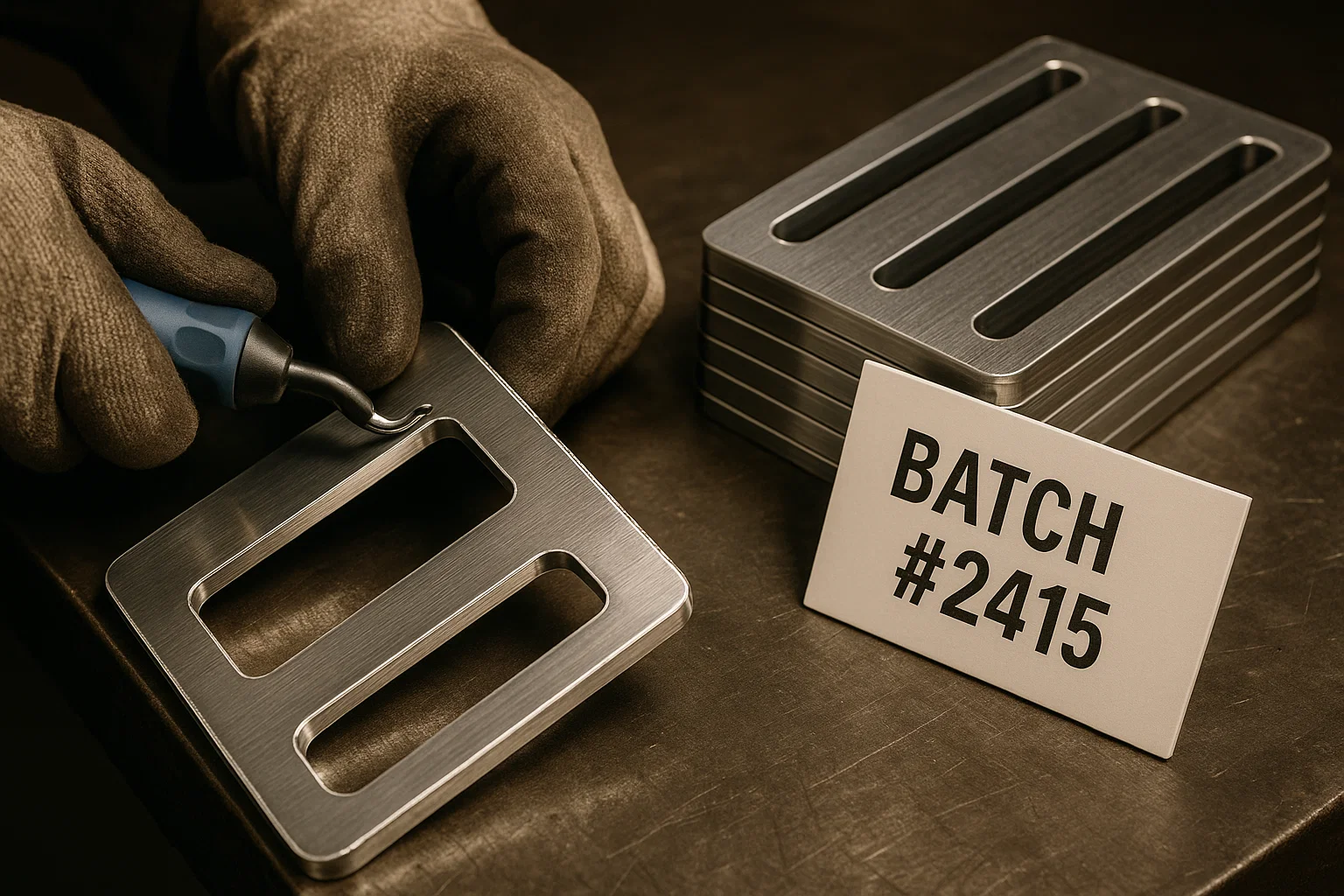
Beyond Cutting: Delivering Fabrication-Ready Parts
It’s not enough for parts to be accurate, they also need to arrive fabrication-ready. Singleton deburrs all cut parts, checks key dimensions and ensures identification marks are added where needed. This saves clients time during welding and assembly, particularly on high-volume runs.
By reducing setup time and eliminating unnecessary rework, our profiling service contributes to leaner production processes and more predictable output. That reliability is what keeps many of our clients coming back for repeat profiling orders.
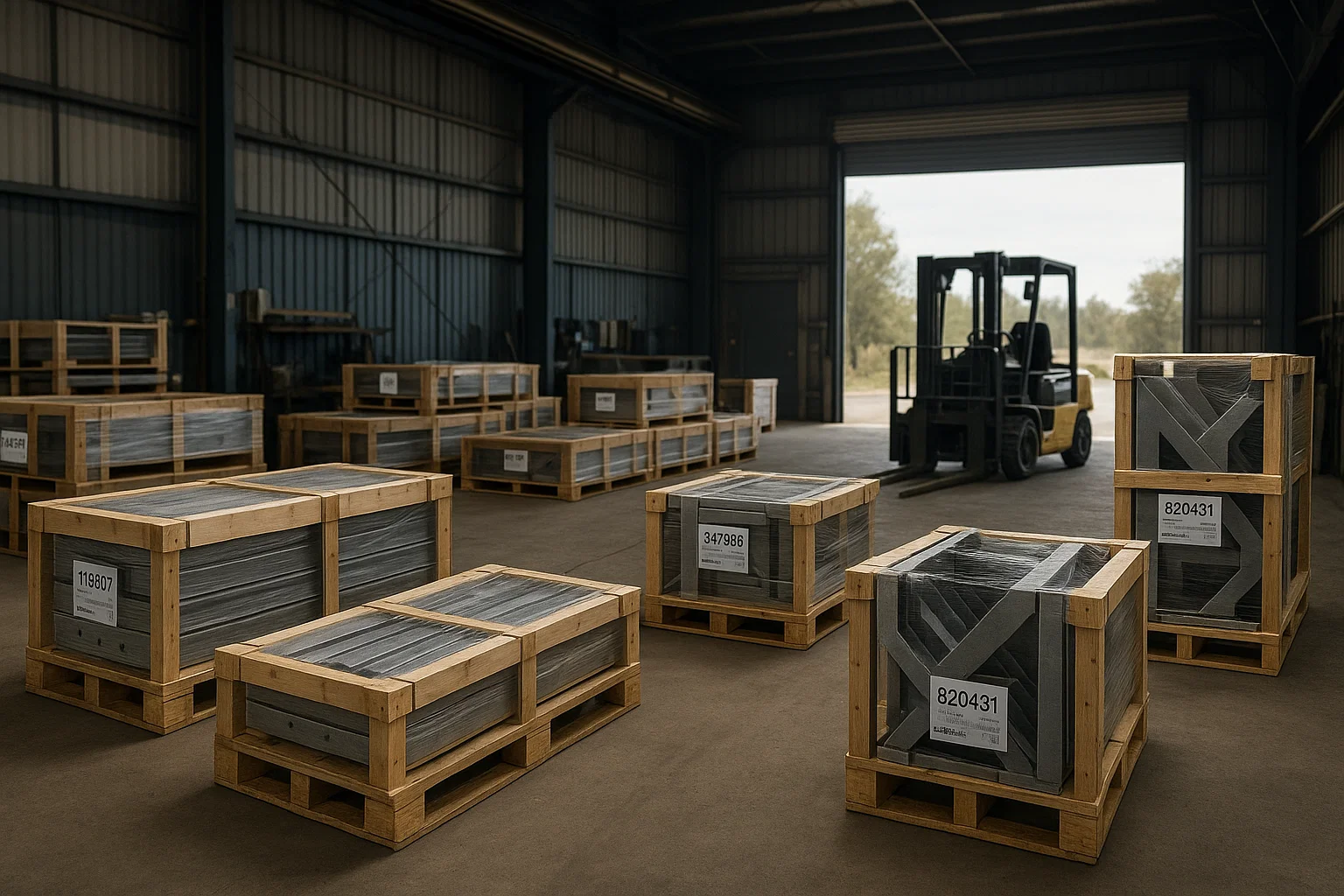
Supporting Production Teams Across the UK
Singleton Engineering supports companies across Greater Manchester, the Midlands and the wider UK with CNC profiling that scales with production. Whether you need 50 mild steel cleats every month or 5,000 stainless components per quarter, we can profile, prep and deliver your parts to spec.
We’re not just a CNC machine shop, we’re a fabrication partner who understands batch work, supply chain pressures and QA compliance. Our work helps clients hit their delivery targets while maintaining their own internal standards.
Why Repeat Profiling Is a Strategic Advantage
In manufacturing, every delay has a knock-on effect. Having a partner who can deliver consistent, accurate steel profiling across every batch gives your business a real edge.
Whether you’re working with high-strength alloys or general-purpose stainless steel grades, Singleton has the tools, knowledge and systems to keep production moving. With repeat profiling, your quality stays constant, no matter the volume.
If you’re ready to streamline your profiling process, reduce risk and improve output, contact Singleton Engineering to discuss your next production run.