In the world of food-grade manufacturing, hygiene isn’t just a bonus, it’s a requirement. Whether it’s a large-scale processing plant, a commercial kitchen, or a bottling facility, the choice of materials can make or break compliance with health regulations. This is where food-grade stainless steel fabrication proves invaluable. Durable, easy to clean and resistant to corrosion, stainless steel is the backbone of safe, efficient and regulation-compliant food manufacturing environments.
It’s not just about using stainless steel, it’s about using it well. That’s where precision metal fabrication makes all the difference.
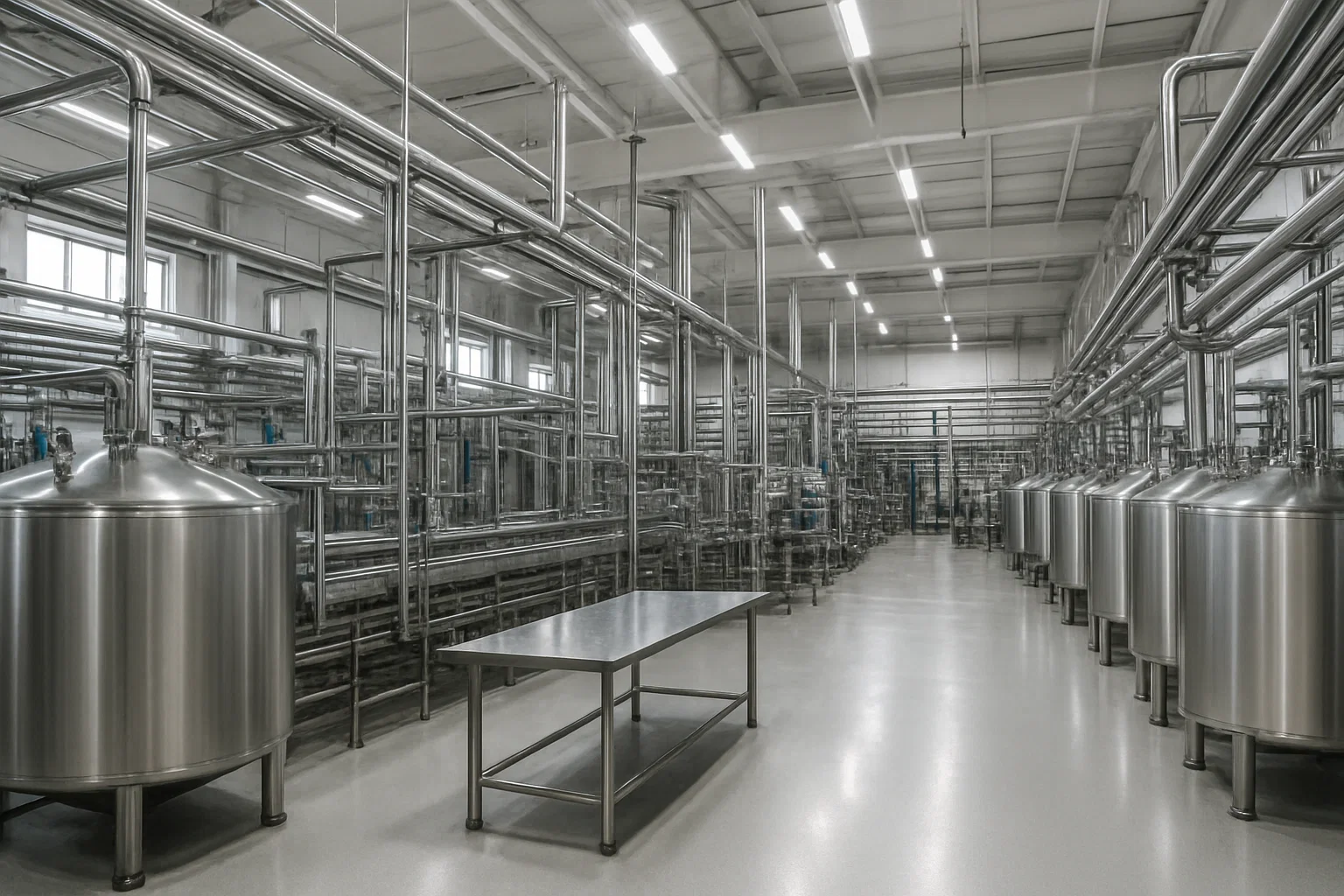
The Role of Stainless Steel in the Food Industry
Stainless steel has long been the material of choice for food processing environments. Its properties naturally align with the demands of food safety.
It doesn’t harbour bacteria, it’s non-porous, so it won’t absorb moisture or odours. Most importantly, it stands up to repeated cleaning with harsh chemicals and high temperatures.
Manufacturers working in food production, whether for meat, dairy, baked goods, beverages, or ready meals, rely on metal fabrication using stainless steel to deliver infrastructure that won’t fail under pressure. From conveyor systems and preparation tables to tanks, hoppers, pipework and guardrails, stainless steel appears throughout the food production chain.
What makes it especially suitable is its compatibility with clean-in-place (CIP) systems and its ability to meet the exact specifications of regulated industries.
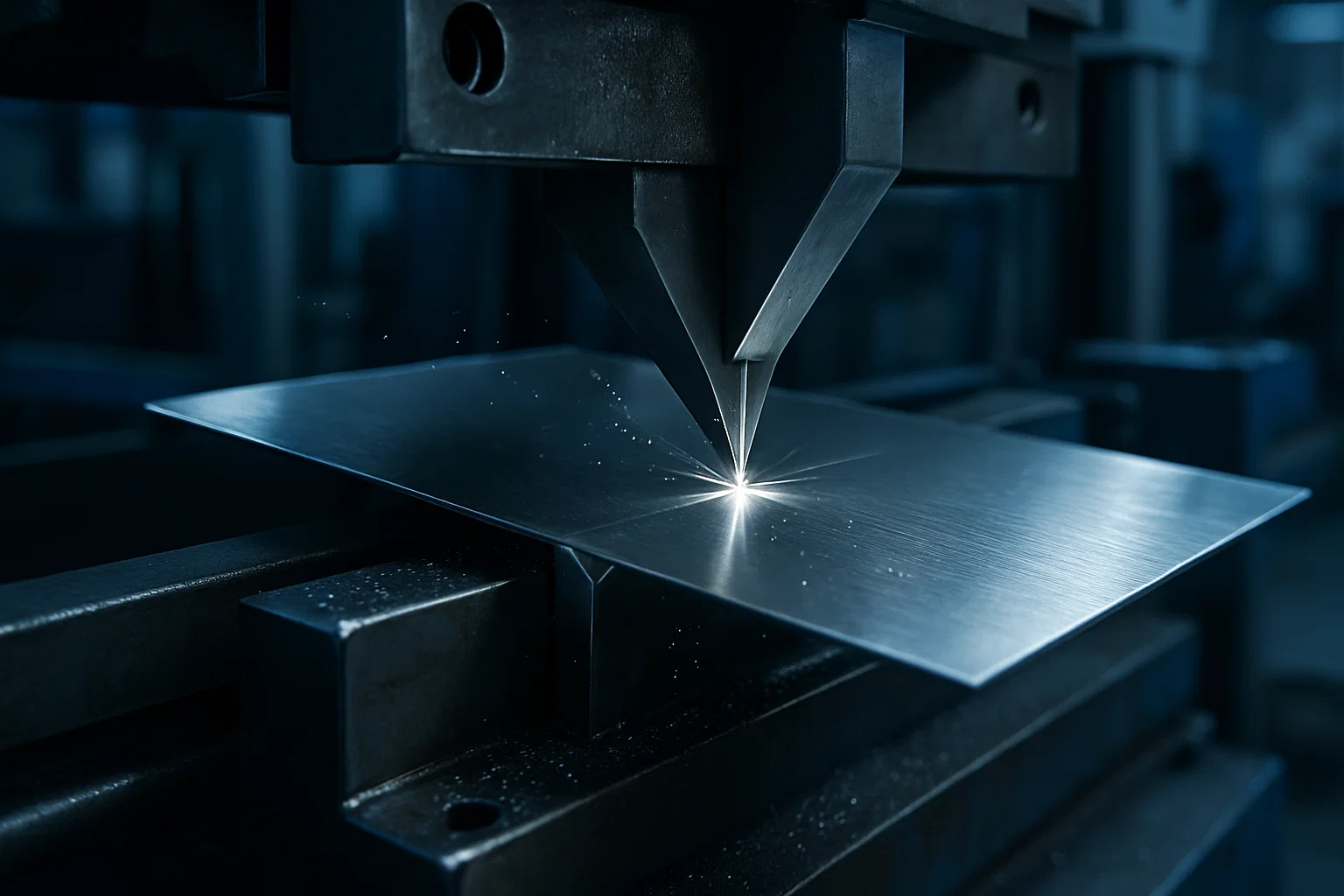
Sheet Metal Fabrication in Food Manufacturing
Much of the work in a food-grade environment begins with the sheet metal fabrication process. Using precision cutting, folding and welding, sheet metal is transformed into trays, housings, guards, splashbacks and panels.
This process allows manufacturers to work with thinner materials while maintaining strength and hygiene. It’s common to use grades like 304 or 316, depending on the environment and whether the equipment comes into contact with acidic foods or cleaning agents.
Singleton Engineering applies sheet metal fabrication techniques to build equipment that meets the needs of busy factories where downtime isn’t an option. Whether it’s a set of custom machine covers or a fully hygienic workstation, the key is always performance, cleanability and long-term durability.
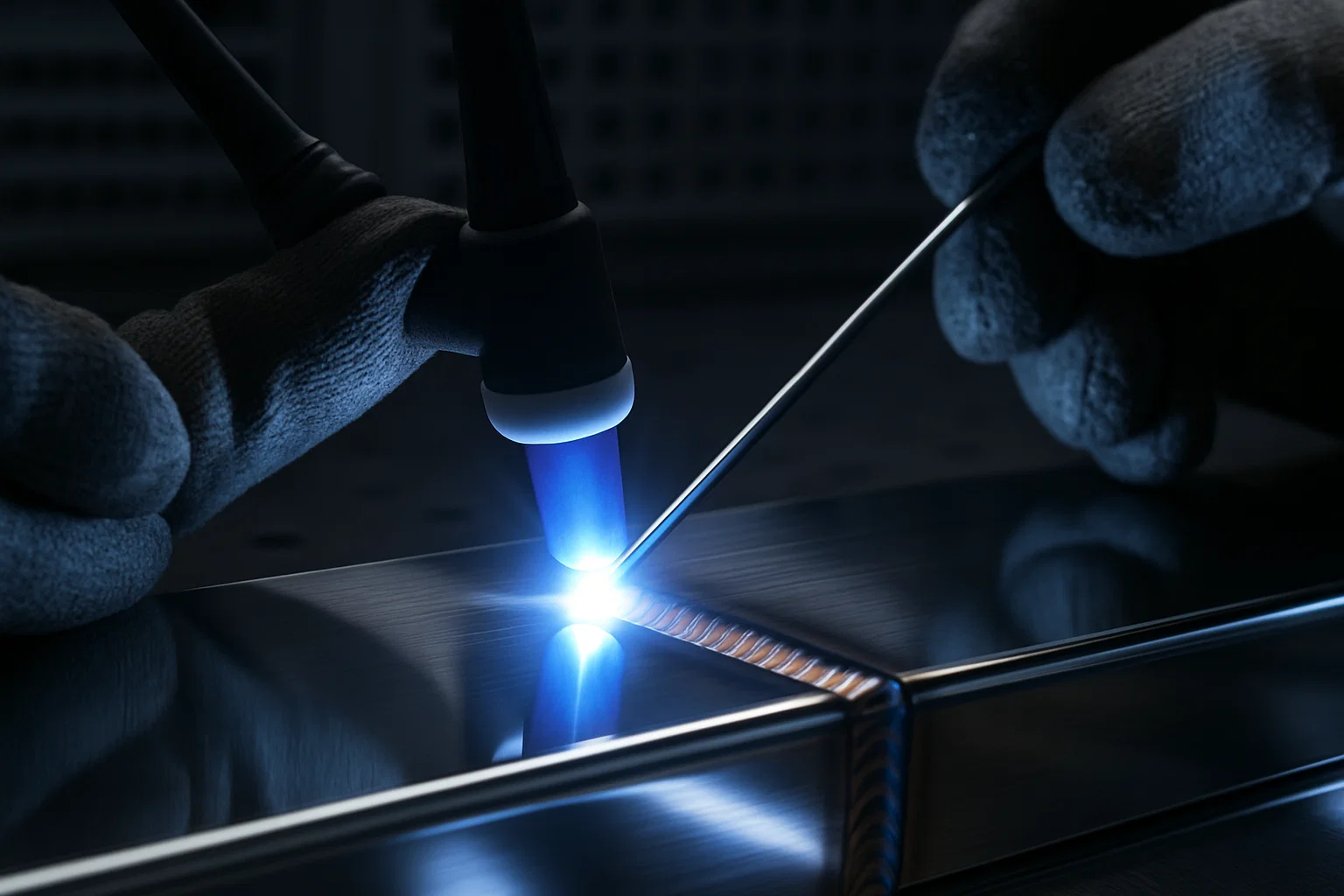
Welding Techniques That Stand Up to Inspection
One of the most important aspects of stainless steel fabrication in food environments is the weld. Poor-quality welds can trap food particles, introduce bacteria and ultimately fail inspections.
That’s why the choice of welding techniques matters. At Singleton Engineering, both TIG welding (tungsten inert gas) and MIG welding (metal inert gas) are used depending on the task. TIG is ideal for fine, precision welds that must be smoothed and polished, while MIG is often used on structural or support elements.
In certain cases, where delicate components need joining, spot welding may also be used. The technique is fast, clean and appropriate for lightweight sheet metal assemblies.
A deep understanding of different welding techniques allows fabricators to select the right approach for each application, balancing strength, hygiene and efficiency.
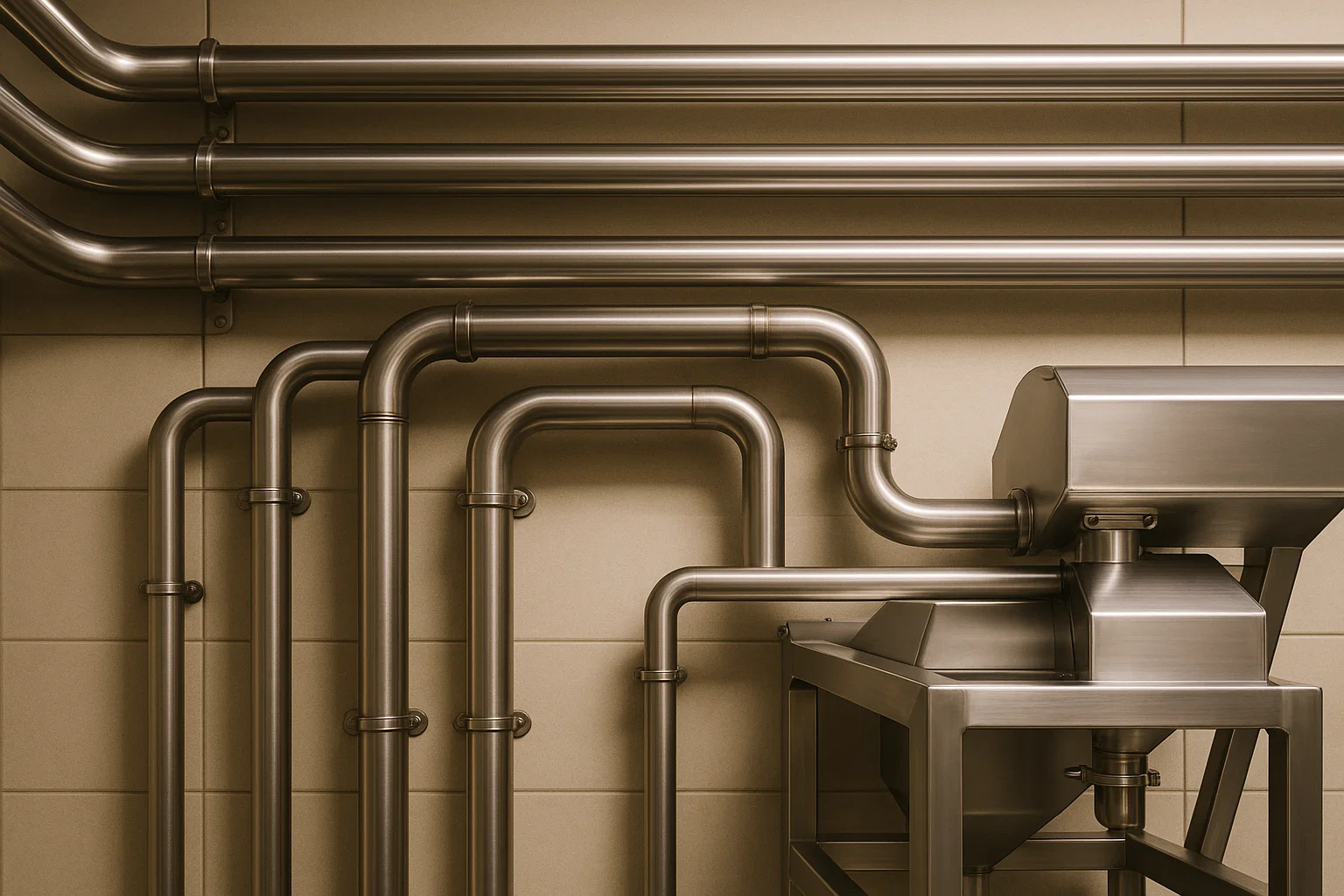
Pipework and Structural Frames for the Food Sector
One of the most frequent requests in this sector is for stainless steel pipework. Whether it’s for transporting fluids, steam, or air, pipework must be both robust and cleanable. In dairy, brewing and food flavouring lines, 316-grade stainless is often preferred due to its corrosion resistance.
Singleton Engineering fabricates structural frames to hold machines, conveyors, or tanks in place. These aren’t just supports, they’re engineered to withstand constant use, frequent washdowns and high temperatures without compromising performance.
Where needed, carbon steel or mild steel may be used for secondary supports or non-contact elements, although stainless steel remains the gold standard for all food-contact surfaces.
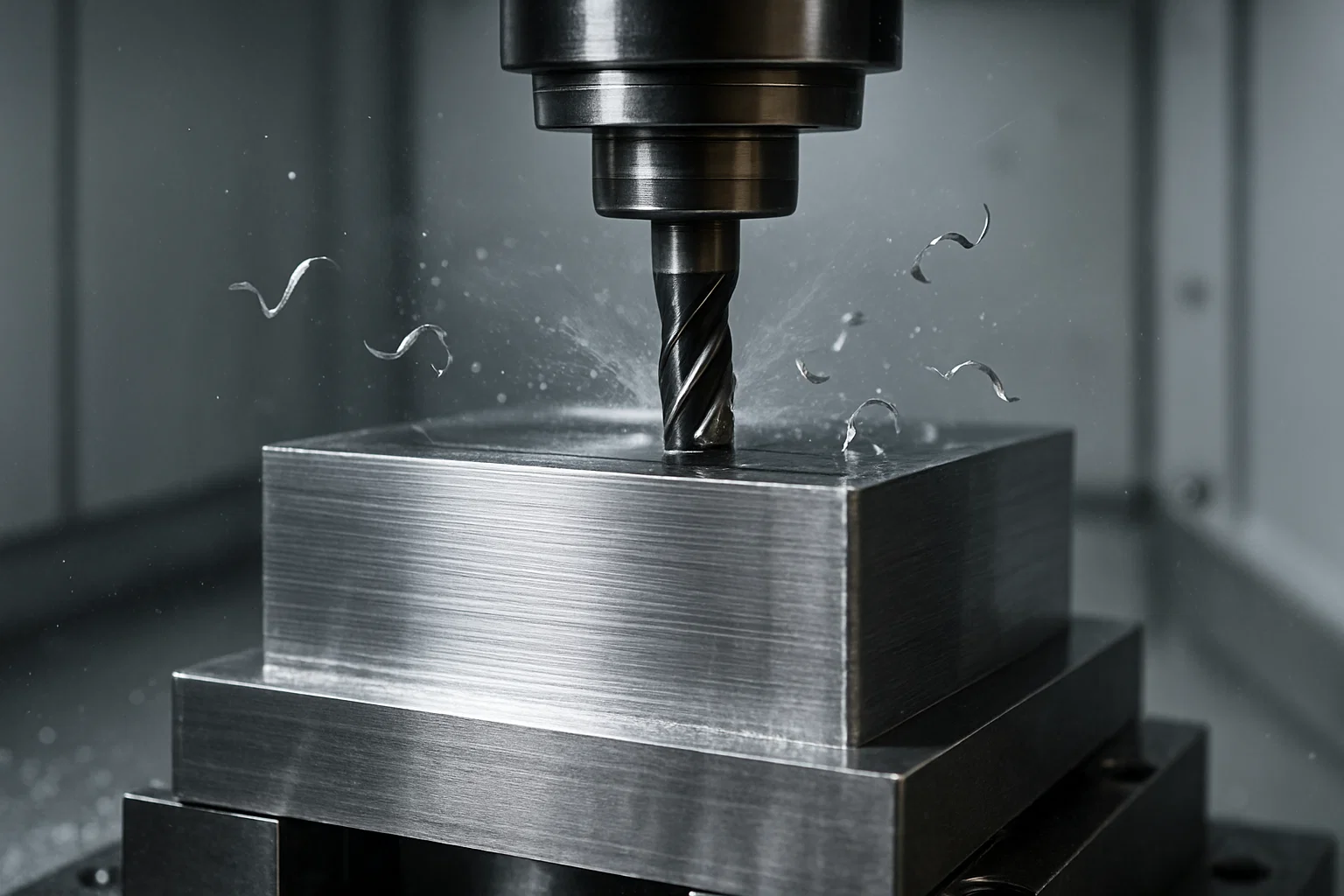
CNC Precision for Complex Components
Modern facilities often rely on CNC machining to deliver components that require accuracy to fractions of a millimetre. This is especially important where parts are integrated into automated systems.
At Singleton, CNC mills and routers are used to create brackets, control panels, mounts and custom fittings. This enables manufacturers to keep operations running smoothly and avoids the risk of machine incompatibility due to off-the-shelf designs.
The ability to deliver machined components that meet exact specifications is what makes a fabricator a long-term partner rather than just a supplier.
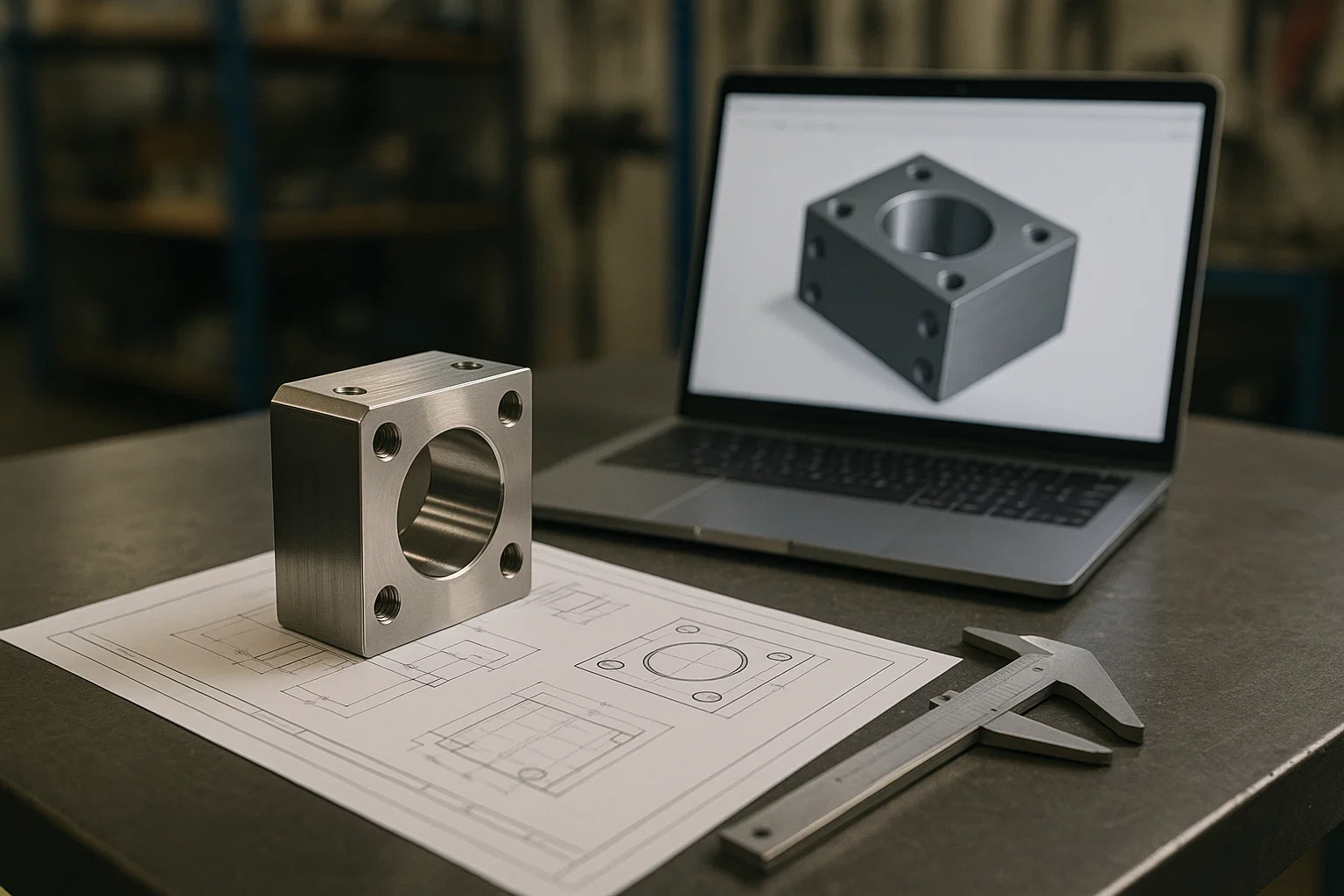
Managing Fabrication Projects from Concept to Completion
In food production, projects need to move quickly. Time lost during install or maintenance can cost thousands in missed output. That’s why effective project management is essential.
From the first site survey through to installation, Singleton works alongside production managers and maintenance teams to ensure every component arrives ready to perform. By providing full documentation and compliance evidence, including finish specs and material traceability, we help clients meet inspection and audit standards with confidence.
This commitment to guaranteed quality has led to repeat work with some of the UK’s best-known food producers.
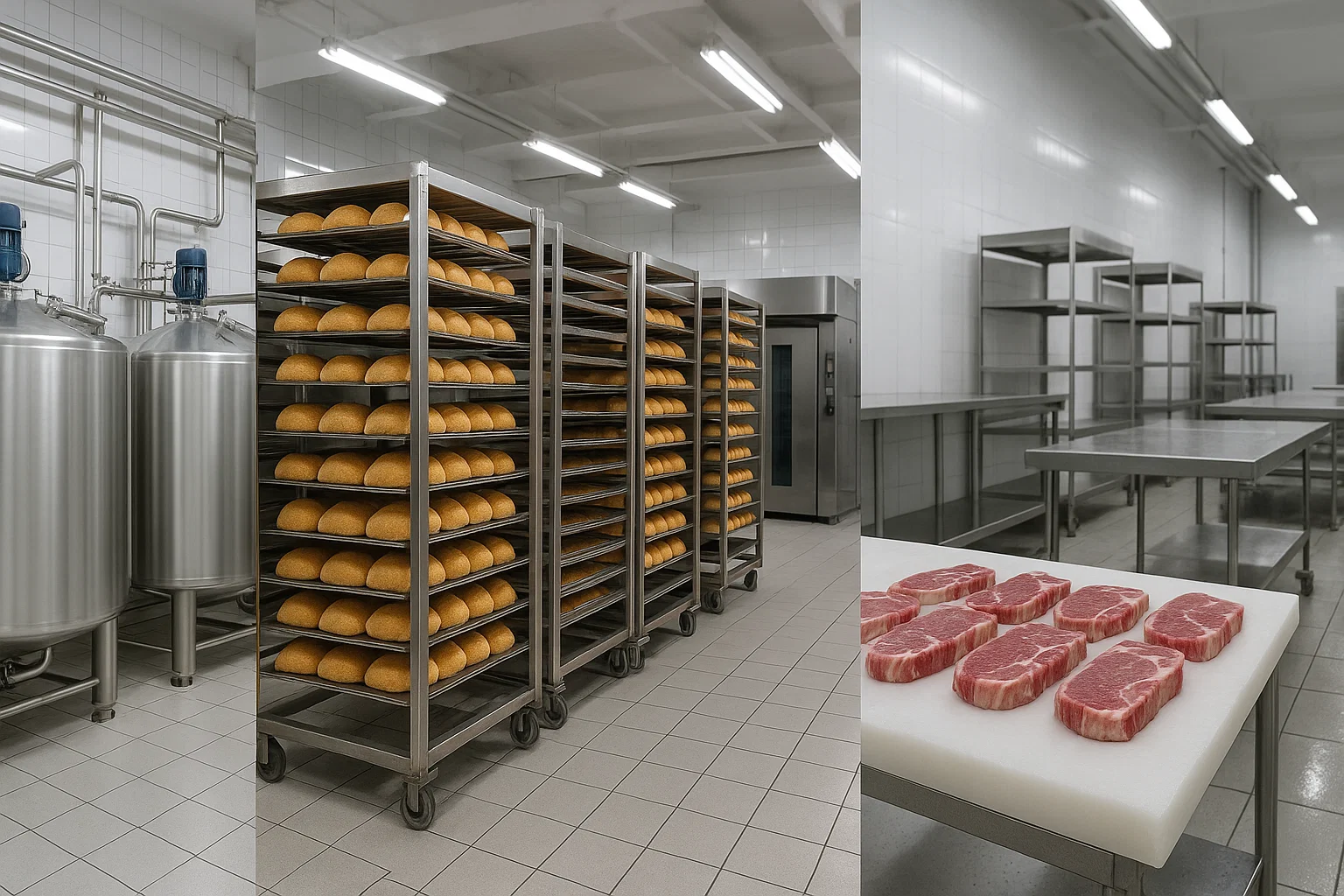
Real-World Applications Across the UK Food Industry
To bring the process to life, here are some real examples of food-sector fabrication:
- Dairies: Fabricated stainless milk tanks, fully polished and sealed to prevent spoilage.
- Commercial bakeries: Heat-resistant sheet metal oven racks and covers with seamless welds.
- Meat processing: Frames and barriers with food-grade finishes, ensuring zero contamination risk.
- Beverage facilities: Custom-fabricated mixing tanks with CIP-compatible pipework and access panels.
All of these projects rely on food-safe fabrication methods that consider hygiene, flow efficiency and space optimisation from the ground up.
A Smarter Material, Fabricated for Performance
Stainless steel isn’t just tough—it’s engineered for demanding environments. In food-grade manufacturing, it supports fast cleaning, long-lasting durability and above all, food safety.
However, great material isn’t enough. To get the best from it, you need smart design, proven fabrication services and a team that knows the food industry inside out.
From initial sketches to final install, Singleton Engineering delivers metal products that meet regulations, exceed expectations and keep food businesses moving.
Ready to discuss your next stainless steel project? Contact Singleton Engineering Solutions for metal fabrication tailored to the food sector.